Pick and place – Important Questions to Consider When Choosing a Pick and Place ROBOT
1.Advantages of Implementing Automation in Manufacturing with Pick and Place Machines:
Automated assembly systems are versatile tools with a wide range of uses, spanning from crafting intricate prototypes to streamlining the production of everyday consumer goods, and even in the intricate assembly of specialized medical and defense electronics.
However, it’s essential to note that while pick and place machines are valuable assets, they are just one facet of the array of robotic part handling solutions found in modern manufacturing environments.
When delving into the specifics of a particular task or operational domain, there’s rarely a one-size-fits-all solution readily available.
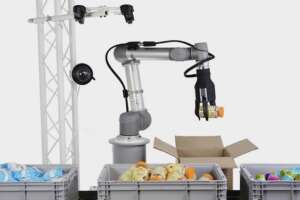
Therefore, it’s prudent to conduct a comprehensive evaluation of production needs and materials before committing to a pick and place robot. Should the prospect of this evaluation seem daunting, our team of seasoned project management professionals stands ready to provide expert guidance every step of the way.
2-What to Consider Before Implementing a Pick and Place Machine
The primary motivation behind investing in assembly line automation is to enhance efficiency. This rationale for automation is succinctly presented in the research of Min Zhou and Renjie Jiang (2022), where they argue that even a mere 1% enhancement in efficiency over an extended operational period can yield substantial economic advantages and reduce overall expenditure.
While the rationale for automation may be evident, pinpointing where efficiency improvements are most needed might not be as straightforward. To address this, here are three guiding questions aimed at contextualizing how the implementation of pick and place automation can elevate the throughput of your specific warehouse or factory:
- Where are the critical choke points in your current manufacturing processes that stand to benefit the most from automation?
- Which tasks in your production workflow demand repetitive or precise actions that could be streamlined through the integration of pick and place automation?
- How can the integration of pick and place automation optimize resource allocation and minimize idle time within your manufacturing facility, thereby boosting overall throughput?
3-How Will a Pick and Place Robot Minimize Reliance on Human Labor?
Over the years, observers and analysts monitoring the progression of automation have consistently foreseen a heightened utilization of and dependence on machinery for production. Initially, when many of these forecasts were formulated, the expense associated with automation rendered it unfeasible for small or medium-sized manufacturing assembly lines.
Nevertheless, as industrial robot integrators have steadily refined their processes, the accessibility of automation in manufacturing has improved significantly, coinciding with an imperative need. Companies have long contemplated the implementation of pick and place machines to enhance coordination in material handling.
In recent times, escalating employment costs have underscored the growing necessity to automate manufacturing processes. A 2022 report by Reuters highlighted a significant surge in labor costs, with a year-on-year increase of 5.1%, marking the largest rise since the inception of the current series in 2001, following a 4.5% increase in the previous quarter. Clearly, the present moment demands the automation of processes to diminish reliance on human labor.
4.How Will a Pick and Place ROBOT Enhance Workplace Safety?
Including this point might seem contradictory given the earlier discussion about the reduction in human labor. However, it’s important to acknowledge that the human element in manufacturing will likely never be completely eliminated, at least not in the foreseeable future. Instead, the prevailing trend indicates a shift towards increased collaboration between robots and humans, rather than outright replacement. Therefore, the implementation of pick and place automation should prioritize enhancing working conditions for the humans involved in the process.
Similar to digital twin technology, which is already integrated into numerous assembly lines to elevate safety and production standards in manufacturing, pick and place automation should also consider adopting vision system inspection. This approach not only facilitates the faster and more efficient movement of physical products along the assembly line but also ensures that these processes are carried out with utmost safety. Investing in safety measures alongside automation undoubtedly benefits companies and their employees, making it imperative to prioritize safety considerations when contemplating automation strategies.
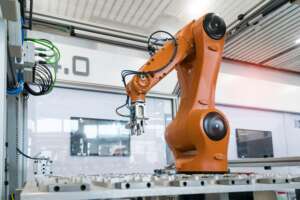
5.How Will a Pick and Place Machine Optimize Warehouse/ Factory Space?
Under the umbrella of “efficiency,” lie pivotal goals centered around enhancing inventory management and optimizing the utilization of available workspace. A pick and place machine serves as a valuable tool in achieving these objectives, directly and indirectly, by expediting product movement with heightened speed and precision. This streamlined operation aids in minimizing surplus inventory, consequently enhancing customer satisfaction, ensuring product line completion, and reducing uncertainties in lead times.
While the placement speed of a pick and place machine can positively influence overall production output, it’s crucial to scrutinize metrics such as components per hour (CPH) or parts per hour (PPH). Evaluating not only a machine’s capacity to handle requisite components but also its efficiency in processing them within a specified timeframe is essential.
Furthermore, to extract maximum benefits from a pick and place system, it’s imperative to analyze the methodology employed for determining the sequence of object retrieval. Machines operate within the confines of their built-in programming and capabilities. Identifying any potential constraints in maneuverability or functionality in advance is crucial to ensuring that the chosen pick and place solution aligns effectively with the specific requirements of your manufacturing assembly line.
Summary:
A pick and place robot is a type of automation technology utilized in manufacturing and logistics operations to automate the process of picking up objects from one location and placing them in another. These robots play a crucial role in improving efficiency, enhancing productivity, and optimizing workflow in various industries.
One of the primary benefits of pick and place robots is their ability to handle repetitive tasks with precision and consistency, reducing the risk of errors and increasing throughput. By automating material handling processes, these robots can streamline production lines, minimize downtime, and improve overall operational efficiency.
Pick and place robots come in various configurations, including Cartesian, SCARA, delta, and articulated arm robots, each suited to different applications and environments. They are equipped with advanced sensors, vision systems, and grippers to adapt to different objects and environments, enabling them to perform a wide range of tasks with high accuracy.
In addition to enhancing productivity, pick and place robots also contribute to workplace safety by reducing the need for manual labor in hazardous or repetitive tasks. They can operate in confined spaces and handle heavy loads, reducing the risk of injuries and accidents for human workers.
Overall, pick and place robots are versatile and adaptable automation solutions that offer significant advantages in terms of efficiency, productivity, and safety in manufacturing and logistics operations. Their integration into production processes can lead to cost savings, improved quality, and competitive advantages for businesses across various industries.
MARKROBOTIC With our profound expertise in plastics manufacturing, we offer tools and systems meticulously crafted to elevate your plastic assembly and injection molding processes to optimal efficiency. Whether you’re navigating plastics applications or injection molding tasks, our product line presents the most comprehensive array of grippers and other end-of-arm tooling devices tailored to meet your exacting requirements. Our extensive selection of readily available, in-stock parts ensures swift delivery. Additionally, we stand ready to collaborate with you in designing bespoke, made-to-fit solutions for your unique process needs, including leveraging cutting-edge 3D printing services. Reach out to us today to embark on your journey towards streamlined plastic manufacturing excellence!
Visit markrobotic.com to connect with our knowledgeable professionals and discover how we can meet your unique needs.
MARKROBOTIC LTD COMPANY Has more than 14 years of experience and is well known for high-performance IML ROBOT ,EOAT System , TOP ENTRY ROBOT , Handle Fitting Machines, Medical Automation Systems as well as innovative downstream solutions that include Product/Decoration Inspection, Assembly-and Box Filling Systems.
Headquarter of MARKROBOTIC is based in Istanbul /Turkey , providing superior service and greater overall value to a rapidly expanding global customer base.
For request you can contact with us : WWW.MARKROBOTIC.COM