Top 5 Advantages of Opting for Electric Injection Molding Machine

All-electric injection molding machines have established a firm presence in the market over decades, offering a multitude of advantages. While standard hydraulic and hybrid machines still find applications, major manufacturers predominantly prioritize the production of all-electric models. This trend is underscored by continual technological advancements, particularly in making larger tonnage all-electric machines more economically viable. The trajectory is evident: the industry’s future lies in all-electric injection molding machines.
Below, we delineate the top 5 reasons endorsing the adoption of this technology for molding processes:
1. Maintenance Ease:
By eliminating the need for hydraulic oil, all-electric injection molding machines simplify maintenance tasks, reducing the likelihood of oil leaks and spills that can disrupt operations and compromise workplace safety.
This streamlined maintenance process enhances operational efficiency and minimizes downtime, ensuring continuous production with minimal interruptions.
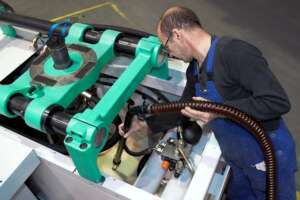
- Oil-Free Operation: A Definitive Advantage :
When evaluating different types of injection molding machines, one crucial distinction lies in their reliance on hydraulic systems. Standard hydraulic and hybrid machines necessitate hydraulic oil to facilitate clamping and injection actions, posing inherent risks of oil leaks and spills. Conversely, all-electric injection molding machines revolutionize this aspect by utilizing servo electric motors for all machine functions, completely eliminating the need for hydraulic oil.
The absence of hydraulic oil in all-electric machines translates to a pristine manufacturing floor, free from the mess and hazards associated with oil leaks. This is particularly vital during mold changes, where slippery oil spills can pose significant safety risks. Moreover, the elimination of hydraulic oil obviates the need for regular oil replacements, typically required every 2 to 5+ years depending on operational factors like continuous usage and elevated oil temperatures that accelerate degradation.
The stark contrast between using and not using hydraulic oil underscores the immense benefits of all-electric injection molding machines.
The avoidance of oil contamination is especially critical in industries such as food packaging ,IML , medical molding, or clean room operations, where maintaining pristine production environments is paramount.
- No More Oil Changes Reduced Maintenance Burden :
The longevity of hydraulic oil in injection molding machines varies significantly based on usage hours and machine quality. In some instances, competitors’ brand-new machines have experienced extreme oil contamination within just six months of operation. The thought of frequent oil replacements, typically required every 6 to 12 months, is daunting, especially considering the substantial costs associated with large machines consuming over 500 gallons of hydraulic oil.
While some customers using hybrid injection molding machines have reported extended oil life, reaching up to 5 years or more with periodic quality testing, manufacturers typically recommend oil changes every 3 to 4 years based on operational hours. Despite potential extensions in oil lifespan, the prospect of regular oil changes remains a maintenance headache and cost burden for manufacturers.
The absence of hydraulic oil in all-electric injection molding machines eliminates this maintenance headache altogether, offering a clear advantage in terms of reduced maintenance requirements and lower operating costs. With no oil changes to worry about, manufacturers can focus on uninterrupted production and improved operational efficiency.
The Clean and Silent Solution for Food Packaging and Medical Molding : All-electric injection molding machines offer an unparalleled advantage for industries with stringent cleanliness standards, such as food packaging and medical molding. With no reliance on hydraulic oil, these machines provide a pristine working environment, free from the risk of oil contamination.
This cleanliness is crucial, especially when preparing for plant audits or delivering parts to customers. The absence of oil contamination ensures that your facility remains spotless and compliant with regulatory standards. Additionally, there’s no concern about sending out contaminated parts to customers, safeguarding your reputation for quality and reliability.
Moreover, the quiet operation of all-electric machines further enhances the working environment, reducing noise pollution and creating a more pleasant atmosphere for employees. In summary, the combination of cleanliness and quiet operation makes all-electric injection molding machines the ideal choice for food packaging and medical molding applications, where hygiene and precision are paramount.
Unveiling Remarkable Energy Efficiency
Despite their name, all-electric injection molding machine is renowned for their exceptional energy efficiency. A direct comparison between a standard hydraulic machine and an all-electric counterpart reveals staggering energy savings of 50% to 70% across most applications.
In a standard hydraulic machine, the hydraulic pump remains continuously active during operation, necessitating constant circulation of oil and generating heat throughout the production cycle.
In stark contrast, all-electric machines consume electricity only when servo motors are in motion. Significantly, a considerable portion of the production cycle, notably during the cooling phase, is spent in idle mode, further optimizing energy consumption.
This inherent energy-efficient design not only translates into substantial cost savings but also underscores the environmental benefits of adopting all-electric injection molding technology.
By minimizing energy wastage and carbon emissions, all-electric machines represent a sustainable solution for manufacturers striving to enhance both their economic and ecological footprint.”
- All Electric Servo Motors:
The stark contrast between standard hydraulic and all-electric injection molding machines lies in their fundamental design and operation. Standard hydraulic machines rely on one or more pumps to generate hydraulic pressure, which is then directed through valves to various hydraulic mechanisms for required movements. Conversely, all-electric machines eschew a central electric motor, instead employing individual electric motors tailored for specific functions such as mold open/close, injection, recovery, and ejection.
This distinction is pivotal: while electric motors in all-electric machines remain idle until their designated function is needed, hydraulic pumps in standard machines run continuously, regardless of ongoing operations. The difference is particularly striking during the cooling phase, where all-electric machines operate with minimal energy consumption while hydraulic counterparts continue to consume energy to maintain hydraulic pressure.
This efficiency in energy utilization underscores the superiority of all-electric injection molding machines, not only in terms of energy savings but also in operational flexibility and precision. As manufacturers increasingly prioritize sustainability and cost-effectiveness, the inherent advantages of all-electric machines make them an indispensable choice for modern injection molding operations.
- No Hydraulic Cooling Needed:
The energy efficiency of all-electric injection molding machines extends beyond their operation to ancillary systems, presenting further opportunities for savings. With the elimination of hydraulic pump circuits, the need for cooling on the hydraulics is also eradicated. Unlike standard hydraulic machines, all-electric machines do not require machine cooling, as they lack hydraulic components.
This absence of hydraulic cooling systems not only simplifies the setup and operation but also translates into additional energy savings. Without the need for hydraulic cooling, manufacturers can forego the installation of additional water lines and the associated permits, further reducing costs. Moreover, chillers, typically used for hydraulic cooling in traditional machines, consume significant amounts of electricity, while cooling towers necessitate water, electricity, and frequent maintenance along with monthly water treatment plans.
By eliminating these cooling requirements, all-electric injection molding machines not only streamline operations but also contribute to substantial cost and energy savings. This holistic approach to energy efficiency reinforces the compelling case for transitioning to all-electric technology, aligning with both economic and environmental objectives in the manufacturing industry.
- Less Equipment Equals Less Maintenance :
Transitioning to exclusively using all-electric injection molding machines often leads to a significant simplification of cooling infrastructure within manufacturing facilities. Since all-electric machines don’t require high-temperature cooling circuits (typically maintained between 85-95°F) for hydraulic systems, customers typically only need chillers for low-temperature cooling needs (usually under 80°F, often set at around 55°F) for molds and feed throats.
This consolidation of cooling requirements offers several notable advantages for manufacturers. Firstly, it results in fewer pieces of equipment, thereby reducing capital investment. Additionally, with fewer components to maintain and manage, upkeep and maintenance costs are significantly reduced. Moreover, the decreased energy consumption associated with operating fewer cooling systems leads to lower overhead costs and improved operational efficiency.
By optimizing cooling infrastructure to align with the specific needs of all-electric injection molding machines, manufacturers can realize substantial cost savings and operational benefits. This strategic approach not only enhances economic efficiency but also streamlines production processes, contributing to overall business success.
- Overall Plant Energy Savings :
The ability of all-electric machines to operate cooler aligns seamlessly with the stringent temperature requirements of medical and clean room manufacturing. By minimizing heat generation, all-electric machines help ensure consistent temperature control within these specialized environments, which is crucial for maintaining product quality and regulatory compliance.
Given these benefits, it’s no surprise that medical and clean room manufacturers predominantly opt for all-electric injection molding machines. Not only do they offer precise control and cleanliness, but their ability to run cooler further enhances their suitability for these demanding applications.
- Think Long Term Savings:
The comparison between a 390-ton standard hydraulic injection molding machine and an all-electric injection molding machine reveals significant annual savings of approximately $17,000 with the latter. These savings stem from various factors discussed earlier, including lower energy consumption, reduced maintenance costs, and operational efficiencies. Moreover, with energy costs steadily rising across the US and Mexico, the projected savings are expected to increase over time.
Considering the long lifespan of quality injection molding machines—often exceeding 20 years—it’s essential to adopt a forward-thinking approach when investing in new equipment. Choosing a reputable and established company that manufactures its own components, such as platens, motors, sensors, breakers, contactors, and cables, ensures ongoing access to replacement parts and support.
By prioritizing durability, reliability, and long-term cost-effectiveness in machine selection, manufacturers can make informed decisions that not only optimize current operations but also set the stage for sustained success over the machine’s extended lifespan.
3. Exceptional Repeatability and Precision:
- Accuracy:
Among the three types of molding machines, all-electric injection molding machines stand out for their superior accuracy and repeatability. This distinction stems from their utilization of electric servo motors, which offer precise movement control with a tolerance as fine as 0.1mm (+/-). Unlike hydraulic machines, where movements are actuated by hydraulic pressure and are subject to pressure curves and fluctuations, all-electric machines deliver consistent and precise movements, resulting in minimal variation and enhanced part quality.
The precise control afforded by electric servo motors ensures that each movement in the injection molding process is executed with unparalleled accuracy, eliminating the potential for deviations or inaccuracies that may arise from hydraulic systems. This level of precision is particularly crucial for applications requiring tight tolerances and consistent part dimensions, such as medical and automotive industries.
- Consistency In Production:
All-electric injection molding machines excel in producing intricate, challenging, and thin-walled components with remarkable precision. They ensure the delivery of highly accurate injections while upholding consistent repeatability regardless of the time of day or seasonal changes.
4.) High Speed :
- Simultaneous Movements:
All-electric injection molding machines are equipped with multiple electric servo motors, each connected to pulleys and belts that drive ball screw mechanisms to execute various machine functions, such as platen opening and closing. One of the distinct advantages of all-electric machines is their capability to perform compound movements, enabling simultaneous execution of multiple functions. This feature often results in reduced cycle times compared to standard and hybrid injection molding machines.
- Instant Torque:
Just as electric cars harness instant torque from their electric motors to achieve impressive speed, all-electric injection molding machines leverage the instantaneous linear motions provided by their AC electric servo motors. With this technology, these machines can achieve injection speeds of up to 800mm per second, delivering swift and precise movements. Additionally, the high output and rapid response of AC servo motors enable all-electric machines to incorporate multi-step injection speeds, further enhancing their versatility and performance in molding operations.
5.) Technology Advancements:
- Extremely Reliable:
All-electric injection molding machines stand out as the most reliable option among the different types of injection molding machines. Unlike standard hydraulic and hybrid machines, which were designed decades ago and often prioritize cost efficiency, all-electric machines typically incorporate state-of-the-art technologies.
The utilization of cutting-edge technologies ensures enhanced reliability, accuracy, and repeatability in all-electric machines. Additionally, these machines operate very quietly, with most running at or below 70 decibels. As a result, employees are not required to wear hearing protection while operating them, contributing to a safer and more comfortable work environment.
Furthermore, the absence of hydraulic oil in all-electric machines eliminates the risk of oil-related issues and reduces maintenance requirements. Combined with energy savings and higher accuracy, all-electric machines offer a compelling proposition for manufacturers looking to maximize productivity and minimize operational disruptions.
In summary, all-electric injection molding machines provide a host of benefits, including reliability, accuracy, energy efficiency, and a quieter work environment. These advantages make them the preferred choice for manufacturers seeking optimal performance and longevity in their production processes.
- Automated Features:
All-electric injection molding machines offer a myriad of advantages, including the elimination of common issues such as sticking valves, deteriorating oil quality, fluctuations in ambient temperature, and noisy pumps. Moreover, many of these machines come equipped with standard safety features to enhance operational reliability and protect both personnel and equipment.
For instance, mold safety mechanisms prevent the risk of crushing parts or foreign objects in the mold, ensuring safe and efficient operation. Additionally, cold screw rotation prevention features mitigate the possibility of inadvertently rotating the injection screw while the plastic is still solidified, preventing potential damage to the machine and molds.
Furthermore, most all-electric machines are equipped with centralized or automated lubrication systems. These systems automatically dispense grease onto critical components such as tie bars, toggle links, and linear guides, ensuring optimal performance and extending the lifespan of the machine. Some machines even feature sensors to alert maintenance teams when grease levels are low, streamlining maintenance procedures and minimizing downtime.
Overall, the combination of advanced safety features and automated lubrication systems enhances the reliability, efficiency, and longevity of all-electric injection molding machines, making them a preferred choice for manufacturers seeking consistent and trouble-free production processes.
In conclusion, the preference for all-electric injection molding machines among our customers is driven by several key factors:
- Exceptional cleanliness: All-electric machines eliminate the need for hydraulic oil, resulting in a clean and safe working environment free from oil leaks and spills.
- Low energy consumption: With their efficient electric servo motors and precise control systems, all-electric machines offer significant energy savings compared to hydraulic counterparts, reducing operational costs and environmental impact.
- Superior repeatability and precision: All-electric machines deliver consistent and precise results, thanks to their advanced closed-loop control systems and linear motion technology, ensuring high-quality output with minimal variation.
- High-speed molding: All-electric machines can achieve rapid injection speeds and multi-step injection capabilities, enabling efficient production of complex and thin-walled parts with minimal cycle times.
- Technological advancements and features: All-electric machines often incorporate state-of-the-art technologies and safety features, such as mold safety mechanisms and automated lubrication systems, enhancing reliability, efficiency, and ease of operation.
Overall, the combination of cleanliness, energy efficiency, precision, speed, and advanced features makes all-electric injection molding machines the preferred choice for manufacturers seeking optimal performance and productivity in their molding operations.
See more : https://www.youtube.com/watch?v=QirKdOGxCKs
Visit markrobotic.com to connect with our knowledgeable professionals and discover how we can meet your unique needs.
MARKROBOTIC LTD COMPANY Has more than 14 years of experience and is well known for high-performance IML ROBOT ,EOAT System , TOP ENTRY ROBOT , Handle Fitting Machines, Medical Automation Systems as well as innovative downstream solutions that include Product/Decoration Inspection, Assembly-and Box Filling Systems.
Headquarter of MARKROBOTIC is based in Istanbul /Turkey , providing superior service and greater overall value to a rapidly expanding global customer base.
For request IML ROBOT OR TOP ENTRY ROBOT you can contact with us : WWW.MARKROBOTIC.COM